April.1941 | Established Morioka Industry Co.,Ltd |
---|---|
August.1988 | Start operation in Kawagoe Manufactures (Totalized manufacturing site in Aichi) |
July.1998 | Acquired ISO9002 |
October.2001 | Acquired ISO14001 |
October.2005 | Established Morioka Industry (Suzhou) Co.,Ltd at Suzhou in China |
November.2006 | Add New manufacture (D Building) at Head manufacture in JP |
November.2008 | 3Established Morioka (Shanghai) Trade Co.,Ltd
at Shanghai in China |
MORIOKA INDUSTRY CO.,LTD
Company Profile
Design development and manufacturing for tooling Cold forging, and manufacture as start to finish production from header & former “Cold forging process” to NC turning & Machining.
We are “VA&VE proposal style company”, based on outstanding process technology and long-term knowledge since established days.
■Capital
9.8 Million JPY
■Representative person
Managing Director Michiho Matsuura
■Employee ‘2017.April
All Member | 140 (Trainee from Oversea 25) |
---|---|
Man | 105 |
Female | 35 |
Average age | 39 years old |
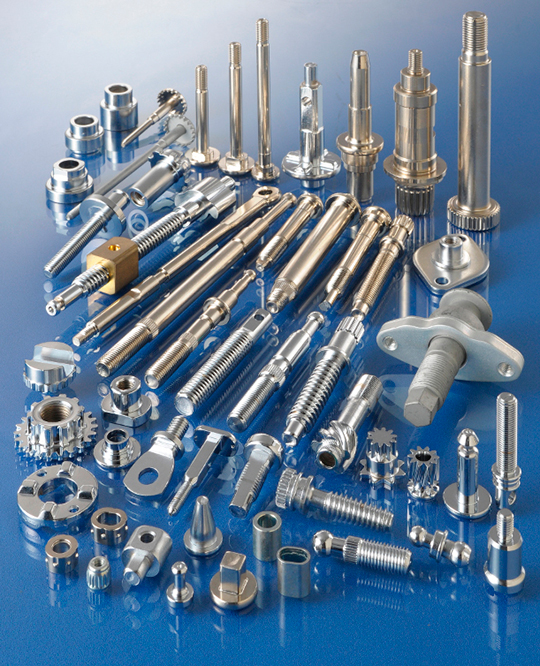
Historical DATA
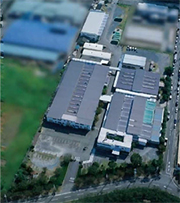
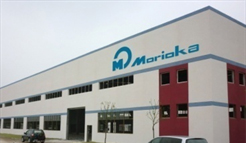
Global Expand Activity
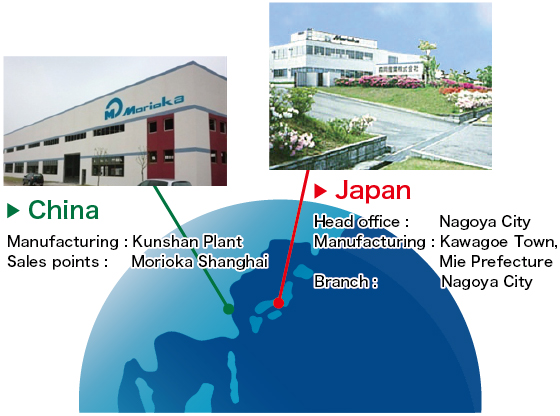
Product-Introduction
Guidance information
Click on the product name in blue to see the details.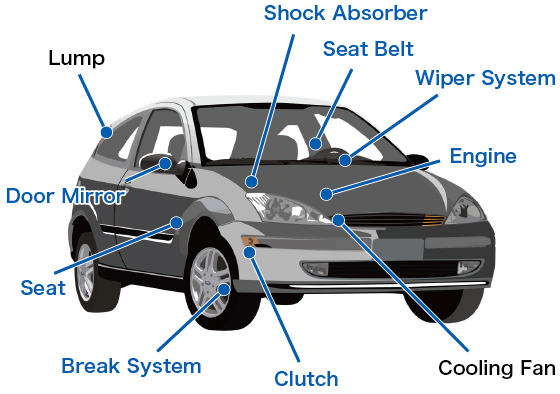
Turn Over
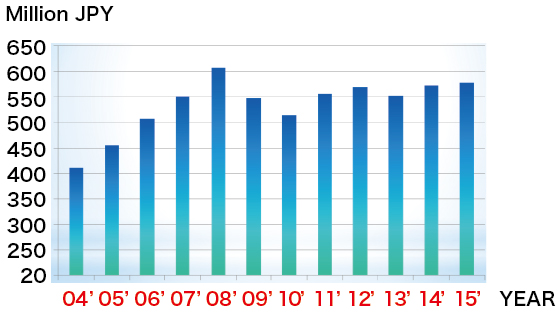
Equipment
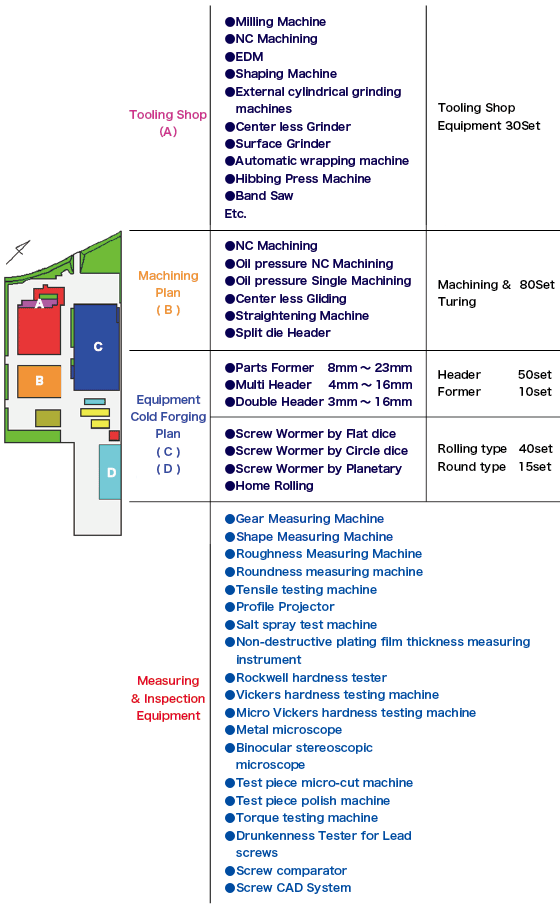
Fundamental Process for Cold Forging
(A)Upsetting
The process to make widen raw material diameter by Punch hitting.
This process adapt to shaping head of Rivet or Bolt.
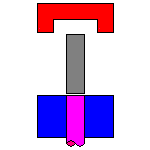
(B)Forward
The process to squeeze raw material by below step.
1st Inserting raw material to tooling for sealed.
2nd Pushing forward raw material by punch.
This process provide big screw result.
(Ratio of Cross-section reduction)
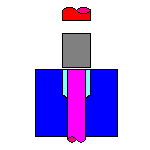
(C)Reductioning
The process to squeeze shaft by punch hitting on the head of extra raw material from
tooling die.
This process provide small ratio of Cross-section reduction.
Generally this process perform with Up setting at same time.
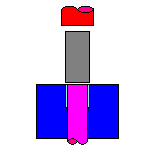
(D)Backward
The process to make Cup shape by Pin pushing material in die, and leading material opposite flow toward pin direction.
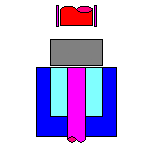
(E)Trimming
The process to make shape by cutting extra material.
This process adapt to hexagon shaping of bolt head.
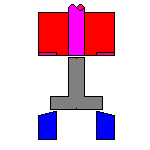
(F)Pierce
The process to make hole by pin.
This process adapt to making hole for Nut.
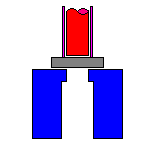
Production machine for Screw
[Double Header]
- Flow steel wire by wire dispatching roller
- Cut Steel wire, hit against stopper, with gross size by Knife
- Move material toward dice
- Make shape by pre up setting punch(1st Punch)
- Make shape by final up setting punch(2nd Punch)
- Push out final product by Knock pin
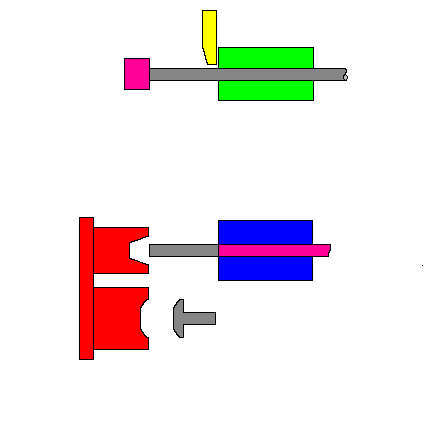
[2 Dice 3 Blow]
- Make shape by pushing material forward in 1st Dice by 1st Dice and 2nd Punch.
- Make shape on same Double header process by 2nd Dice and 2nd.3rd Punch.
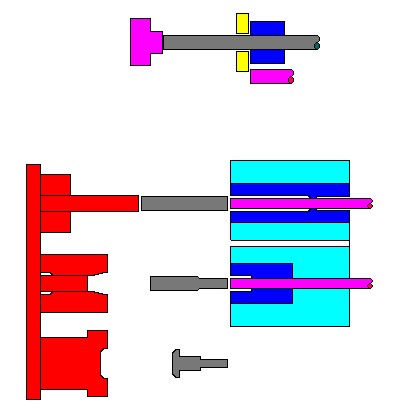
[6-Stage Parts Former]
- Flow steel wire by wire dispatching roller
- Reverse material after shaping on 1st/2nd Dice stage.
- Make pipe shape by 4th Dice and Pin.
- Make Flange shape by 5th Dice.
- Make through hole by 6th Dice and pin.
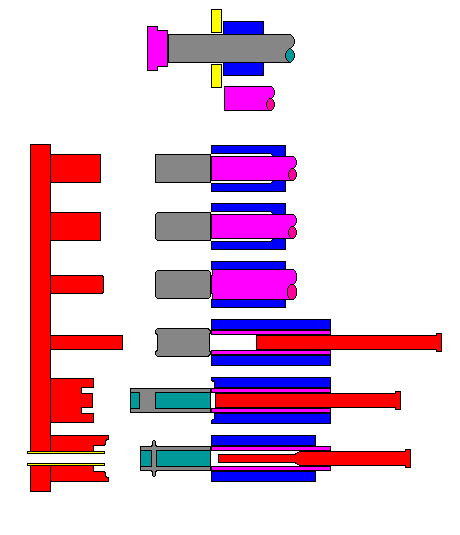
[Rolling machine by Flat dice]
- Roll material with pushing toward roll dice.
- Cut material into thread of dice.
- Gradually make shape screw shape.
- Finish to make complete screw shape.
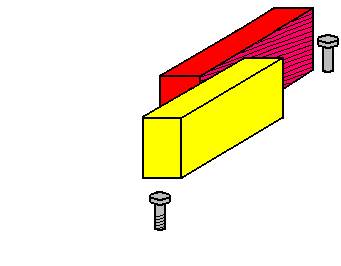
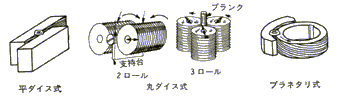
Product Introduction in detail
Break System
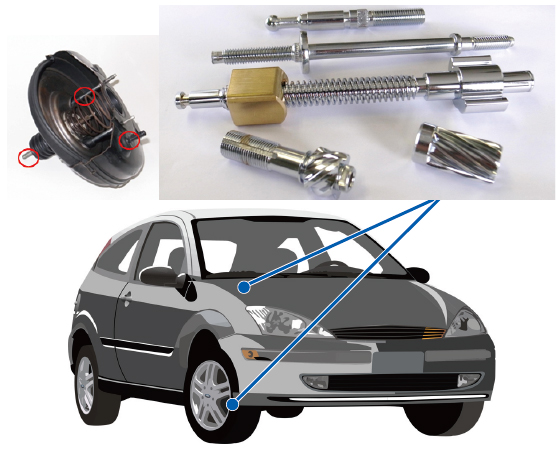
Wiper System
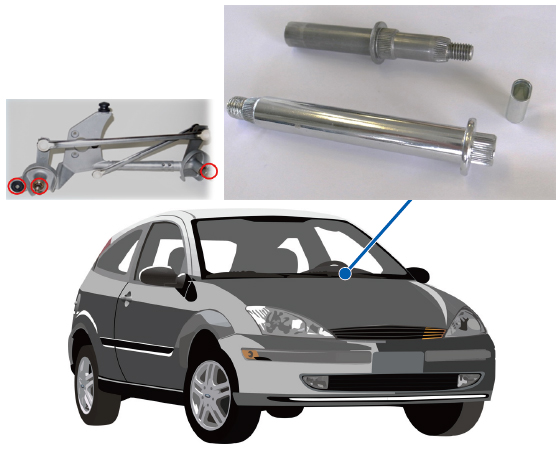
Door Mirror
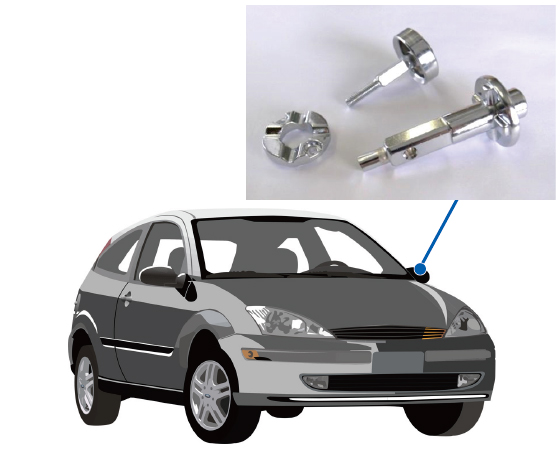
Seat Belt
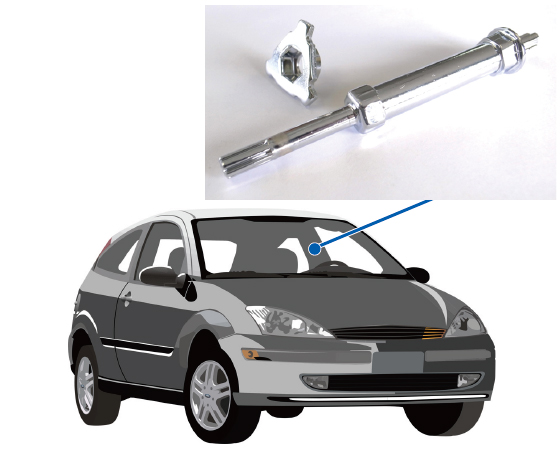
Shock Absorber
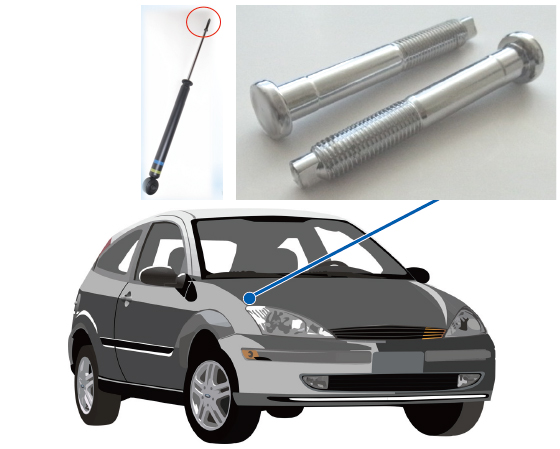